GM TAKES ON THE ENERGIZER BUNNY
This article is from our archives and has not been updated and integrated with our "new" site yet... Even so, it's still awesome - so keep reading!
Published on Mon, Apr 12, 2010
By: The LACar Editorial Staff
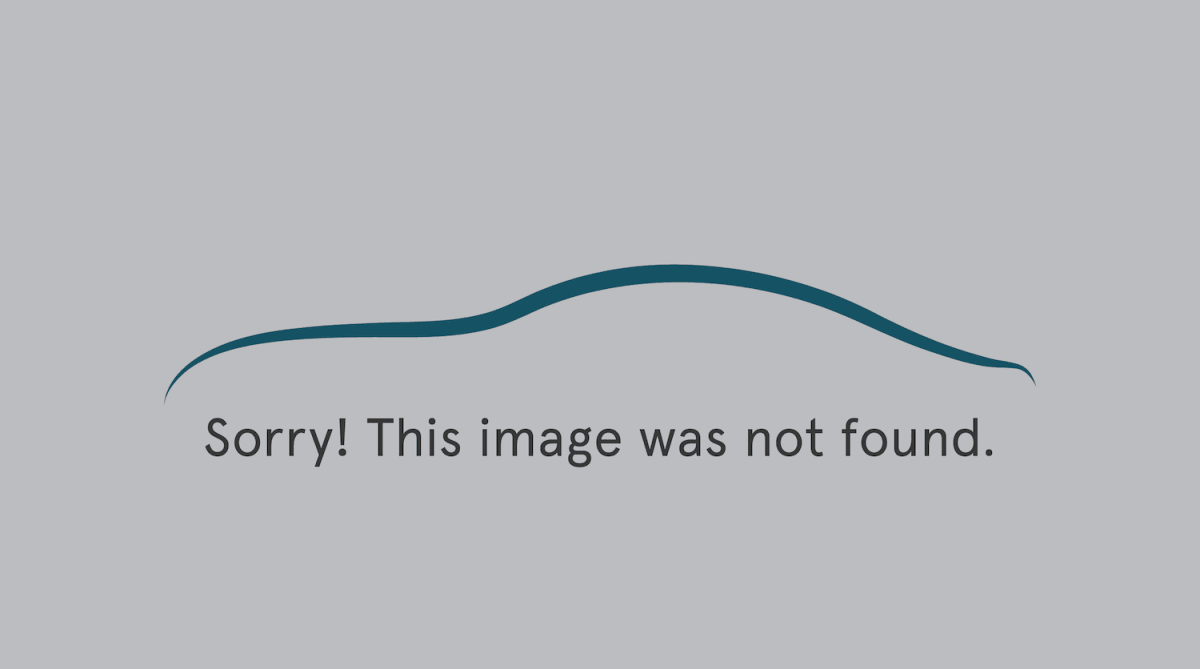
GM battery recipient Volt GM Doubling Size of Most Technologically Advanced Automotive Battery Lab in the United States WARREN, Mich. – General Motors is doubling the size of the largest and most technologically advanced automotive battery lab in the U.S. to expedite the development of electrically driven vehicles for consumers. The $8-million investment will improve on-site testing of all current and new battery cell, module and pack technologies by enlarging the Global Battery Systems Lab on the GM Technical Center campus by 30,000 sq. ft. to 63,000 sq. ft. The addition will be located adjacent to the existing lab inside the Alternative Energy Center facility. Areas previously used for engine testing will be renovated for battery development, with construction beginning this month and scheduled for completion in the summer. “GM is building on its commitment to lead the development of electric vehicle technology – from battery cell design to the charging infrastructure – and today’s investment furthers our work in this area,” said Micky Bly, GM executive director, global electrical systems, hybrids, electric vehicles and batteries. “This addition will benefit consumers by helping us put cleaner, more efficient vehicles, including the Chevrolet Volt electric vehicle with extended range, on the road more quickly and affordably.” GM’s Global Battery Systems Lab began operations in January 2009 and became fully operational in May 2009. It is used by GM’s growing team of more than 1,000 engineers working on advanced batteries and electrically driven vehicles. More than half of the current lab is dedicated to testing the electrochemical battery cells and their enclosures, known as modules. The lab’s remaining floor space is committed to evaluating completed battery packs. “We’ve made the commitment to design, develop, validate and manufacture automotive battery technology in-house,” said Bly. “Consolidating these testing capabilities at the Global Battery Systems Lab will reduce costs, provide a competitive advantage, quicken the pace of development and ensure we will design, build and sell the world’s best vehicles.” The Global Battery Systems Lab equipment and test automation systems are being integrated with GM’s global network of battery labs, including Mainz Kastel, Germany and Shanghai, China, to facilitate seamless data exchange and work sharing. http://www.gm.com/experience/technology/research/news/2009/csl_092409.jsp The Global Battery Systems Lab recently received world-class accreditation from the ISO-certified American Association for Laboratory Accreditation (A2LA), a nonprofit, public service group that evaluates the competency and capability of labs across all fields of testing. Auditors from the A2LA reviewed testing procedures and results, equipment calibration, operations documentation, personnel competency and the lab’s quality policy. The benefits of being an ISO-certified lab include: ensuring that data is accurate and avoiding expensive retesting from unreliable results. The lab is equipped with 176 test channels and 49 thermal chambers duplicating extreme real-world driving patterns, hot and cold temperatures and calendar life. This lab includes many environmentally conscious features such as a center hallway with high-efficiency LED lighting and a floor made from recycled tires. Approximately 90 percent of the electricity used for battery testing can be returned to the local energy grid for use by homeowners and businesses. The Global Battery Systems Lab received an honorable mention for Green Project of the Year by the Construction Association of Michigan. Additional benefits offered by the Global Battery Systems Lab include a thermal shaker table for testing the structural integrity of the battery and electronic controls; a battery teardown area for failure analysis and competitor benchmarking; an integrated test automation system and improved Design of Experiments methodology – an information-gathering exercise that allows GM to perform more thorough battery tests more quickly. In addition to battery labs in Warren, Mainz-Kastel and Shanghai, GM also has facilities dedicated to vehicle electrification in Honeoye Falls, N.Y., and the GM Technical Center’s Research Chemical Engineering facility.