Reflecting on GM Oshawa
Published on Mon, Jan 20, 2020
By: Brian Kennedy
What’s left of a century of manufacturing jobs? Where does everyone go from here? Those who lost jobs, those who live in the town, and the car buyer, who might not think that such a change has anything particular to do with her or him.
Oshawa, Ontario—To many who labored for decades at the Oshawa General Motors assembly plant, the following was an even exchange: They would build cars, and in turn “the Motors” would reward them with strong wages and great benefits. And to make turnabout fair play once more, they would then build a community. They would be the strong pillars who coached hockey, soccer, and baseball; volunteered; drove cancer patients fifty kilometers to Toronto for treatment and helped fund cancer research through donations; and did other charitable work.
For a century, it happened that way. Those days officially ended in mid-December, when the final truck rolled off the line and all but 300 employees were laid off, not to return. Those remaining will be involved in the manufacturing of parts for GM.
What’s left of a century of manufacturing jobs, in other words, is a relic. The question is, where does everyone go from here—those who lost jobs, those who live in the town, and the car buyer, who might not think that such a change has anything particular to do with her or him.
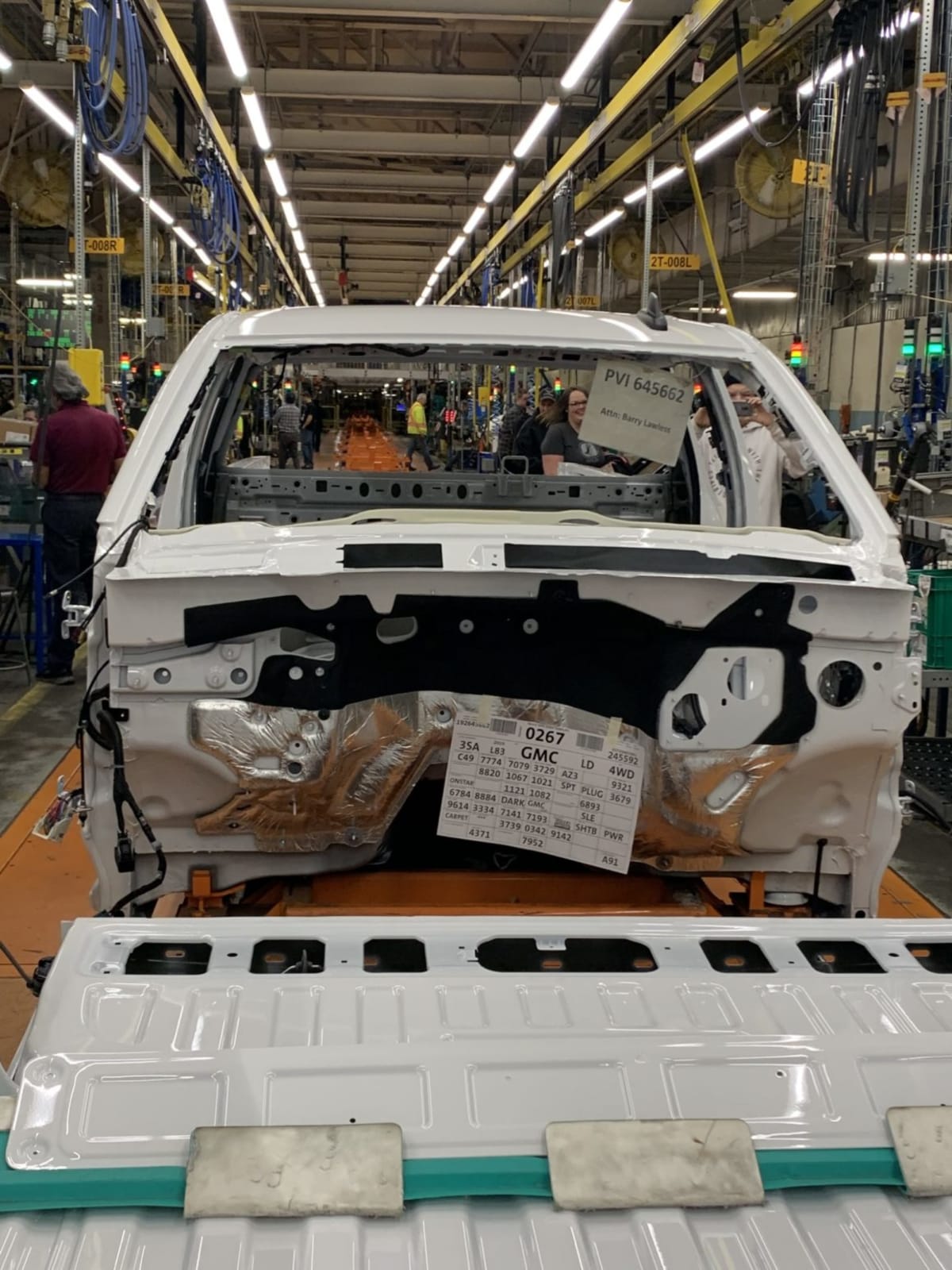
For the city of Oshawa, 45 minutes from downtown Toronto, with a population of about 160,000, this marked a change, but not a massive one as might have been the case in prior years. Rather, this transition had been a long time coming, the slow erosion of manufacturing jobs happening in fits and starts, and sometimes waves, since the 1970s and culminating with the 2008 economic crash. After that, jobs went south, to both the US and Mexico, and Canadian union workers were left without positions despite their government having contributed billions of dollars to the auto sector bailout of the era.
In total over the century that saw vehicles built in Oshawa, approximately 20 million units were constructed. Even up to the end, the plant was producing world-class, award-winning cars and trucks, including, recently, the Chevy Camaro and the GMC Sierra pickup. The Camaro is now made in Lansing, Michigan.
For decades, the capacity of GM and the factory’s hunger for subassembly components meant that there were jobs in many places around town other than the factory itself. Everything from seats to batteries were made locally. That has dwindled, too. A few years ago, for instance, one former plant site was razed, and the environmental damage of battery manufacturing cleaned up. Nearby, a Costco store now features a full parking lot almost all the time.
The loss of this industry is not just the loss of auto-sector jobs, but ancillary ones. This means that everyone from local party supply companies to places which sold lunches and donuts to feed hungry workers were tossed into a turmoil, though the impact of the latest, and final, layoffs was less than would have been caused in the heyday, when tens of thousands of men and women worked in the industry and jobs were essentially handed down from one generation to the next.
The latest change was not without controversy and effort. The local GM workers’ union, Unifor, tried everything it could over the past year to keep things going in Oshawa, according to a recent report in Oshawa This Week. This included ad campaigns, picketing, and posting signs around town to raise awareness. Obviously, none of it worked, as several thousand workers tightened their last bolts and saw nothing behind a white GMC Sierra truck except an empty line as production wound up.
Don’t feel sorry for Oshawa, itself, however. The city has transformed itself into both a commuter town for Toronto-based workers (because housing here is still reasonably affordable compared to Toronto) and an emerging tech hub led by the presence of UOIT (University of Ontario Institute of Technology) also called Ontario Tech. Oshawa will be fine, in other words, despite relegating its manufacturing jobs largely to the past.
But what about those who gave their working lives to the General? Are they tossed aside as relics, too?
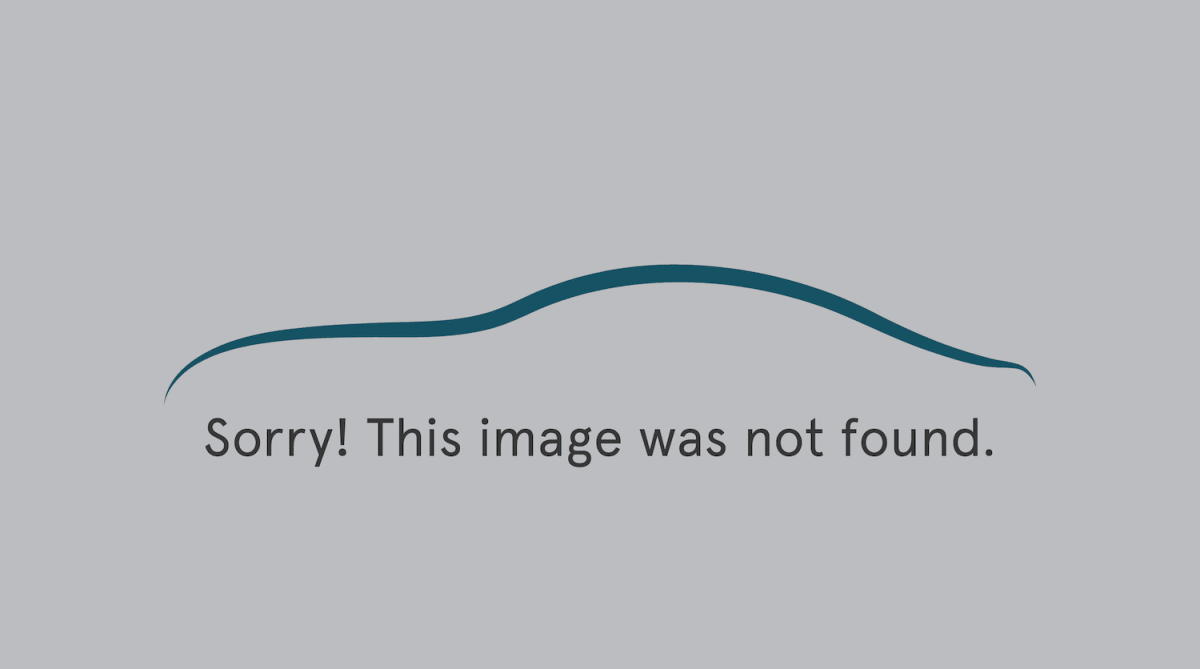
Steve Conway, who worked at the plant in a variety of capacities for more than three decades, gave LACar.com some insights. Conway was an assembler who worked his way up to being a team leader working with the Global Quality Audit Team (GCA). He spent time in Michigan at GM facilities as part of this responsibility.
Conway signed on at General Motors in the mid-1980s after earning a college degree in graphic design. He had worked for GM for a couple of summers while a student. At the time, the company would sporadically hire workers to full-time posts. He thought he’d do it for a decade, but it turned into a career.
The job was tough at times, Steve said as he explained that in those early days, 463 cars were built per shift. The work could be taxing, with repetitive motion injury, often caused by using impact guns with a severe kick, not uncommon.
Through this era, workers were slowly brought into the process of building the best vehicles possible as the Japanese idea of “kaizen” (continuous improvement) was adopted in North American manufacturing. Oshawa consistently received awards for their skillful assembly techniques and reliable products.
Conway described the process and product: “As far as plants go, our plant was the most award-winning plant in North America. And right to the end, our last truck off the line the other day, our truck plant was running the highest quality of the truck plants of any trucks GM was building, in Mexico, in Fort Wayne, Indiana, and in Flint, Michigan.”
Along the way, robots and computers came to play a part in manufacturing, often taking the harder jobs, according to Conway. “They had the jungle line in the body shop, which was with all the wires hanging down, all the welding guns, and guys would have to go and have to hit the welds themselves. They would know where they were supposed to hit, so they would take the gun up and down the wheel well to weld the frame and fender in place. Then [those jobs] went robotic.”
He indicated that technology cost jobs, but that there was a fair tradeoff made: “A lot of jobs were lost to robots, but a lot of the harder jobs were lost to robots, which wasn’t a bad thing.”
Conway speaks with pride about what he built. “I love our vehicles. I’ve rented many others over the years, and they were like tin cans, sardine cans. GM builds really good vehicles. I still love them, and we’re still buying them. You know, there are a lot of people out there who said they’d never buy GM again if [the plant] closed, but I still can’t imagine buying something else right now.”
Could this shutdown have been alleviated? Steve points out that the company has allocated product to Mexico and China as well as the US and Korea. “GM has thirteen plants in China, though most of the product made their now stays there, but who knows when that could change?” he says.
What caused the loss of GM Oshawa, Conway says, is “mostly allocating product to Mexico. They could have given us that new Blazer. They’ve run every different sized vehicle that GM builds through our plant, and they all fit. They can run through paint shop. They can run down our trim lines. They can run through the body shop. We can build anything GM makes, so it’s all about allocation, and that [responsibility] goes to the higher levels of the company.”
Think about this, and listen to Conway’s passion: “The allocation—if we’ve got all the awards for quality, and we’re efficient, and we were the most efficient plant as well . . . the most efficient truck plant in North America, highest quality truck plant, and on and on . . . when you’re pumping out 750,000 vehicles a year like in the early 1990s,” he trails off, but the end of the thought is obvious: This decision makes little sense, especially to those most affected.
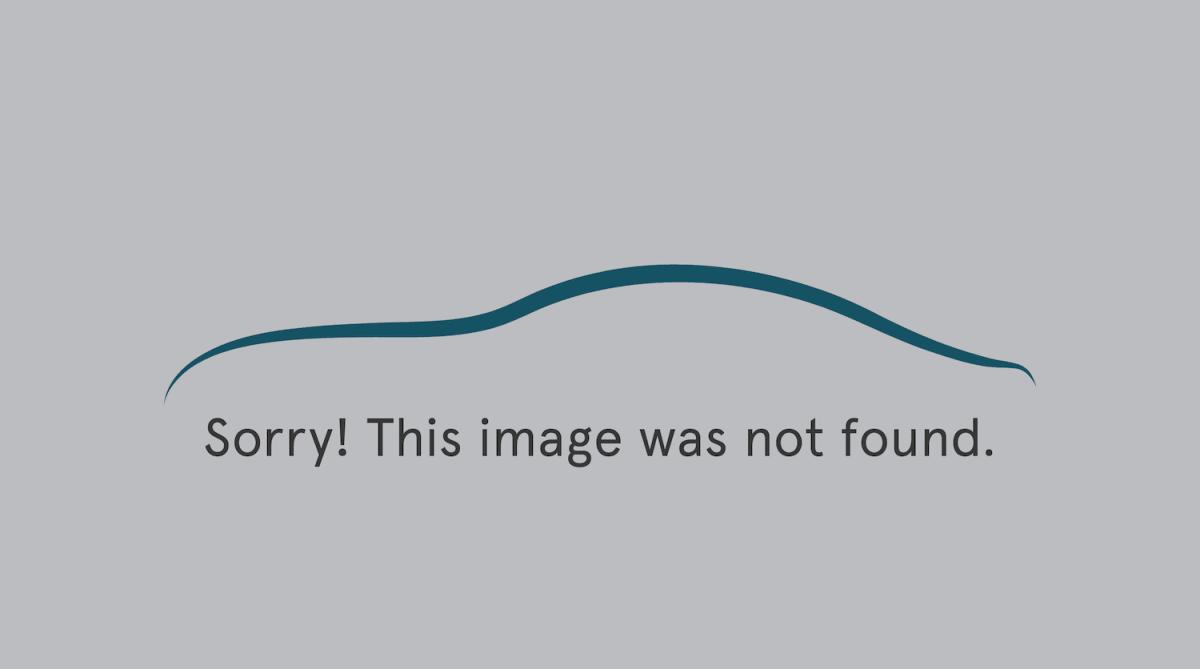
of an era for GM in Oshawa.
But it’s over. To get to the nitty gritty, many workers are being helped to find jobs elsewhere. Those who had enough service time in to retire were offered two options: let their pensions remain in Union control and take monthly dispersals, or take a lump-sum payment and structure their investments under individual control. Their health benefits will continue to be administered by the union. There are some who wonder whether the money in the healthcare kitty will hold up as long as they need it to. Only time will tell.
What will remain of the community the workers at GM Oshawa built? Conway says that Facebook groups exist and that reunions will happen from time to time, but that the Union Hall might have to be given up.
Hopes for the plant and its manufacturing capacity also exist, though they seem a bit far-fetched at present. A December 21st article in another local weekly, The Oshawa Express, entitled “Optimism Remains Despite Assembly Plant Closure” explains that a local coalition group called “Green Jobs Oshawa” wants public ownership to take over the plant and manufacture electric vehicles, amongst other things. The union, Unifor, hasn’t endorsed such a plan, and Jerry Dias, the group’s national leader, was not at the rally held by Green Jobs Oshawa on the day the plant closed. Local government officials, the article says, have expressed support for a return of some sort of auto production to Oshawa, but no concrete plan is in place.
So for now, the message is twofold: rest in peace, Oshawa’s old days, and thrive, those 33,000 who still remember the history of Unifor Local 222 because they lived it.